- Picking Stock
- Printing
- Quality Control
- Additional Branding
- Consolidation and Dispatch
Picking Stock
The first part of the process is to pick your blank stock for orders in the Platform. This can be done multiple times a day.
Log into the Platform and under PRODUCTION > JOBS you can see all pending order batches. For stock picking you are only interested in batches in the “Pending Production” status. You can select one, multiple or all of these batches and under bulk actions select “Download Picking Labels”.
Stock picking labels are printed grouped as logically as possible to make picking easier.
The standard stock picking label size output by the system is 100 x 35mm, an example of this is here - https://www.aalabels.com/roll-labels/rectangle/c1122/

Heat resistant stock picking labels - Labels should ideally be purchased as Heat Resistant as we are dealing with heat presses and drying on Kornit machines and this will mean the labels do not come off during any processes.
Using a site like the below you can cater to your needs depending on the label printer purchased.
100 x 35 mm recommended - LINK
------------------------------------------------------------------------------------------------------------------------------------------------
Label Printer - for stock picking labels - There are a large volume of suitable printers available and part of this depends on the type of labels you settle on, heat resistant labels generally require Thermal Transfer printers which are more expensive at their initial cost but add the benefits to production already detailed in this report. It is important to ensure you buy labels and printers compatible with each other taking into consideration factors such as maximum media width and core diameter for example. The following link is one is just an example - LINK An example of our standard stock picking label is below.
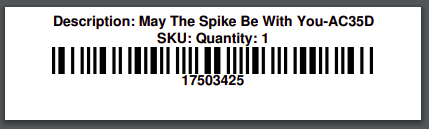
It is recommended to set the “Stock Picking” label option under Documents in the dropship companies advanced setting to “Standard By Item Quantity”. This option allows the system to print one stock label pet item quantity on the order so each item can have its own label.
Printing
So you now have your stack of garments by the Kornit ready to print. Assuming you have completed the setup to ensure the browser downloads into the QuickP hotfolder mentioned in the “Setting up Order Manager and QuickP” section above then the process for printing is simple.
- Ensure your machine running the printer is logged into the Platform and the Print Station Scanpoint - https://platform.kornitx.net/v3/floor/item-print
- Use a barcode scanner (codebar) or type in the number from the stock picking label on the garment you need to print.
- This will bring up a screen showing you a preview and details of the area that you need to print
- Either scan the screen (only works on imaging barcode scanners) or hit the “Print Artwork” to download the artwork to the hotfolder. This will have the naming convention from the above sections.
- Load the garment onto the Kornit Table and print.
- Remove the garment and pass through any drying process you have.
Using this feature we can now set the ability for a KSF override file to now appear on a job template.
Quality Control Station Setup
The next scan point when items come off the drying process is Quality Control (QC), this is an important step because it allows operators not just a quality check touch point but also on screen guidance about the next step in this products production cycle.
On scanning the item you will be able to see previews and details of each print areas status.
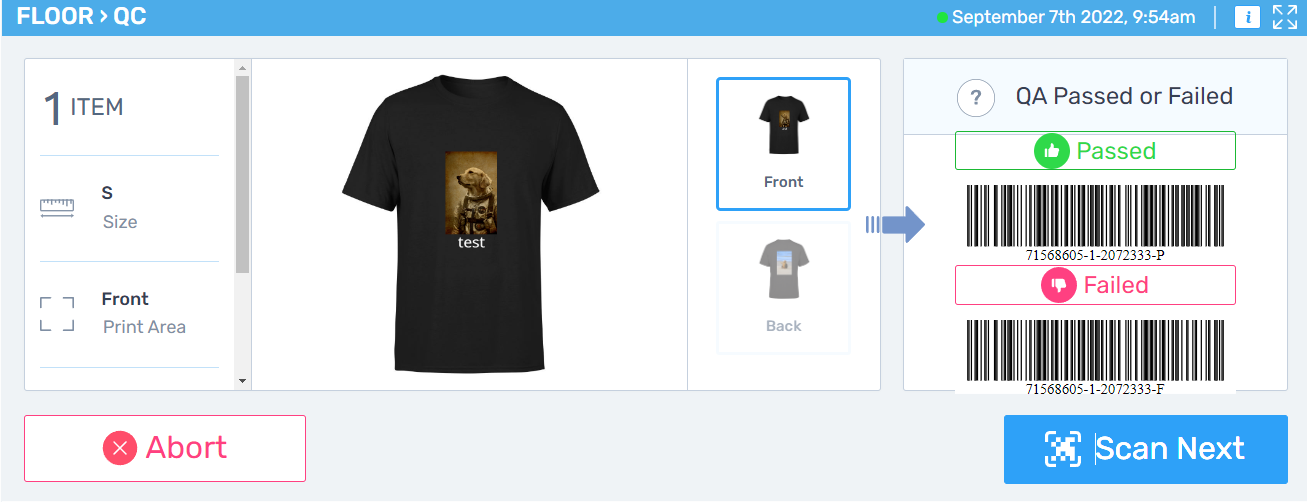
On this example the T-Shirt in question has 2 print areas, Front and Back.
- Front is in the status “IN PRODUCTION”
- Back is in the status “PENDING PRODUCTION”
To the operator they can know from this that the FRONT print area needs to be checked BUT that the product has another area needing printing so they can pass the garment back to the relevant print operator for further decoration.
To proceed with the QC of each area the QC Operator just needs to select the relevant area on the left, this will bring up a screen specific to that area with 2 large barcodes which can be scanned or clicked to pass or fail.
On fail a popup will appear to select a reason and the item will go into the “QC Query” status which should be monitored and managed by production managers.
On pass the status of the print area will change to QC Passed. When all Print areas on the item are in QC Passed the QC screen will give a visual cue as to where the operator needs to take the item in one of 2 options
- Proceed to Branding
- Proceed to Shipping
Additional Branding
This step is strictly optional but in some workflows does add a very valuable step.
The Platform has the ability to run branding stations. For example if you had a requirement to apply different branded or item specific hangtags or neck labels to garments this step can manage that for you seamlessly.
From a setup perspective this should be done through attribute sets. Each unique set of branding elements should be added to an attribute set
So for example 2 sets might be:
Set Name - Disney Garments
Attribute 1 Name - Hangtag
Attribute 1 Value - Disney (bin 29)
Attribute 2 Name - Neck Label
Attribute 2 Value - Disney (bin 30)
Set Name - Marvel Garments
Attribute 1 Name - Hangtag
Attribute 1 Value - Marvel (bin 108)
Attribute 2 Name - Neck Label
Attribute 2 Value - Marvel (Bin 12)

These attributes can be anything that might be item specific, it could be branded packaging, advertising material etc etc.
Each product in Product Manager can have an attribute set allocated to it in the E-Commerce & Data section under “Branding Attribute Set” as shown below.
As long as the product has a set allocated to this it will trigger the branding station step to be available on the workflow.
Images can also be applied to each attribute to give a visual representation (for example a picture of the neck labels)
The Shipping Station in the next step always follows branding so any item that has branding completed should be passed over for shipping.
Consolidation and Shipping

The Shipping scanpoint is where we connect into all of our integrated couriers and aggregators to book in and get your shipping labels / paperwork (Shipping integrations are optional but recommended).
The scanpoint will allow multi item orders to be consolidated by providing a bin number where the item should be put until the remainder of the order is complete - a more in depth article on bins and their setup is available here - Link
When scanning single item orders or the last item on the order the Platform will show a label for printing which should be applied to the box and assuming we are connected to your courier the item will be booked in with them and ready for collection. Any tracking details will have been automatically added to the order and fed back to any retailers needing to be aware of it.