Introduction
Within Floor there is an optional purpose built station to manage Quality Control of your orders called the QC Station. This station allows for finished items print areas to be reviewed against order information and thumbnail images to ensure quality and accuracy for your customers.

Items can either pass or fail this station, passed items move onto the next stage and failed items are rebatched to be produced again.
Regarding which of the Floor workflow the QC station can be used with these are detailed in the workflows 1-7 which are detailed here - Link
How Do I Access The QC Station?
Users with the correct subscription can access the QC Station by following the next few steps. Please note that this will be included within your Kornit X workflow.

Your login will have been provided to you before signing into the system
- Once signed in you must head to the QC Station page which is located within the Floor menu
Once the QC Station is loaded you will see the following screen shown below.
Within this screen you can either begin scanning your items ready for QC or entering in the allocated barcode to run QC on the individual items one at a time. More details on how items can be added and what to do are detailed within the next section of this article.
How Does The QC Station Work?
Once the label for your order has been printed you will be able to scan the barcode. Please note the station accepts Job Item Barcodes with the prefix " ", it can also work in short run mode by scanning the Item ID with the prefix "01". Below is an example of an item within the QC station.
As you can see above, we have one item loaded within the station listing the Size, selected Print Area, Colour and the SKU. In the next part of the screen we can see the entire Print on the Product Print area followed by the most important part of this station - the options to either pass or fail the Order.
Passing an item in this station will signpost to the next workflow station which could be branding or shipping depending on the product settings. Selecting Fail for an item however, allows you to select a reason for reporting. An example of this screen when failing an item can be shown below.
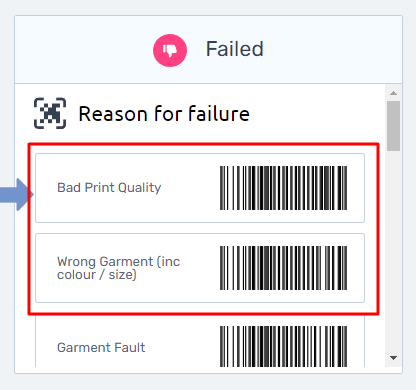
The failure reasons that can be selected are the following - Bad Print Quality, Wrong Garment (Inc colour / size), Garment Fault, Missing Print Area, Wrong Print Position, Artwork Issue, Fixation Stain, Banding, Ink Coverage, Ink Drops, Incomplete Print, Scattered Image, Registration, Colors Bleeding, White Spiking, Off Centre or Spots
Once an item has been failed it will automatically be sent back to be rebatched and sent back through the QC Station, while passed items will move on over to the next station required within your set up workflow. An example of this is shown below, you will be told to move onto the next station with your workflow to progress the item. For the below example this is to move over to the Shipping Station which is next in the sequence.
This station is critical in Kornit X Floor workflows which print multiple times on the same item as it is here where this is signposted, items cycle though print and QC per printable area until all printing is completed at which point it is allowed to move to the next station.

A useful option on the Kornit X QC Station is the fullscreen mode. Where a single computer is going to be used only for that station it allows a cleaner view with now room for error or switching, it keeps focus on the stations intended purpose. Fullscreen mode can be toggled on and off using the icon in the top right of the station which looks like the below.
FAQS
We have included some Frequently asked questions regarding the use of the QC Station which can be found below.
I am unable to access the QC Station?
If you are unable to see either the Floor Modules entirely or the QC Station within this is likely due to user permissions- it could either be that your user/company do not require the QC Station for your workflow. The best way to resolve this is the contact the Kornit X Support team who can confirm what access you need to have and if missing they can amend your users to access the station for you.
The Barcode I am using is not working?
Please ensure that the barcode you are either scanning or entering begins with "03" - if it doesn't this means the barcode you are using is best working with V2 of the platform which is likely which workflow you are using. This should be a very rare occurrence as the workflows most commonly used now are built for V3 of the platform.
I have failed an item in error what should I do?
The best option here is to run through and rebatch the item as you can only pass or fail an item with the QC station once. This is to ensure there is an audit trial on errors which can be reviewed and logged within the history of each item.